NEW! Cordis Proportional Pressure Controls
Clippard Cordis
Resolution in Proportional Control
Proportionally controlling the pressure or flow of gasses and fluids to perform various functions is prevalent in laboratories and manufacturing environments. Often, it is imperative to use products that provide the best resolution. But what is resolution, what does it indicate in proportional control, and what might it mean for your application?
What is Resolution?
Resolution in proportional control applications has context when distinguished from accuracy. Most proportional controllers offer higher resolution than accuracy, but few can claim to be high-resolution devices. Resolution defines the smallest measurement change detectable, while accuracy expresses the deviation of the measurement from the actual value. For example, a pressure transducer may detect pressure fluctuations of 0.1 psig, but the accuracy of the sensor may only be ±2.0 psig. If we record measurements of 99.9 and 100.0 psig, we confirm a pressure change of 0.1 psig, but the sensor's accuracy indicates real pressure to be somewhere in the range of 98.0 to 102.0 psig.
Clippard's high-resolution Cordis series defines resolution as the smallest value of command change that impacts actual pressure response. The Cordis proportional microcontroller employs Clippard proportional valves and proprietary algorithms to deliver 5 mV resolution or better. For instance, a Cordis calibrated 0 to 10 VDC equals 0 to 100 psig realizes pressure changes of 0.05 psig throughout the entire range. With a resolution of 0.05%, the Cordis offers a control ratio of 200:1, signifying 200 steps of resolution for every 1-volt increment. The reason most proportional controllers in today's market do not publish a resolution specification is because their internal proportional valves only achieve steps of 25 mV, and most digital valves step in 50 mV increments or higher.
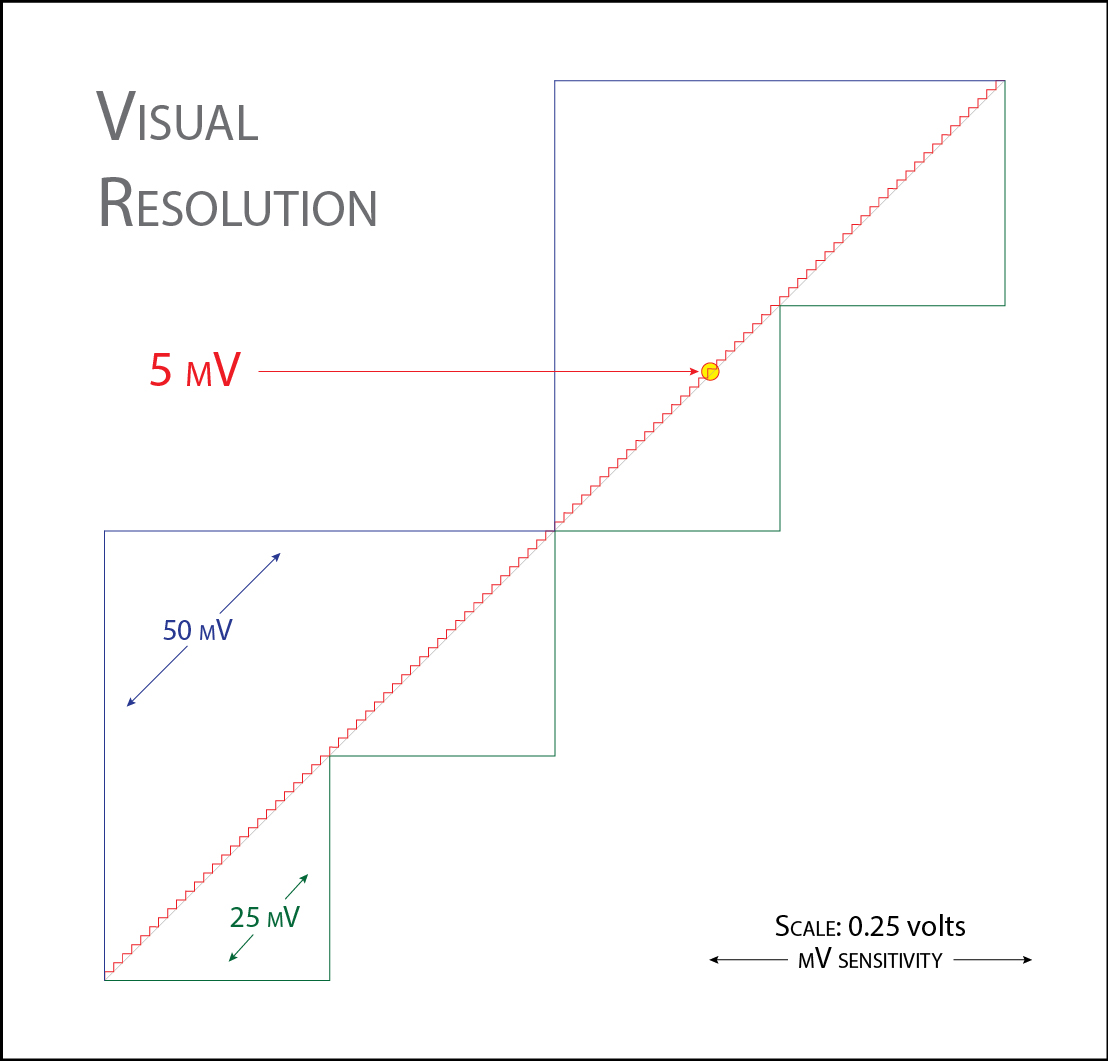
Why Does Resolution Matter?
High-resolution proportional control for many manufacturing and industrial processes may not be essential. However, applications in life sciences, instrumentation systems, and numerous laboratory processes rely on the subtle nuances produced with high-resolution control. Without the ability to provide a smooth ramp to a process, make tiny changes in pressure and flow or react to subtle dynamic process conditions, many applications would not be possible. High-resolution control delivers the ability to count individual cells; print bio-materials such as bone, skin, and organs; or examine and identify individual compounds in gas mixtures.
For years, the practice of hematology has provided tests that evaluate and diagnose a variety of blood conditions, leading to faster, more targeted treatments. Once a condition is identified, flow cytometry is employed to understand the extent of the condition. By measuring the physical and chemical characteristics of individual cells, flow cytometry furnishes cell size, cell count, morphology, DNA information and the existence or absence of particular proteins. These measurements become possible with high-resolution control of the pressurized cell-carrying fluid.
Similar to flow cytometry, gas chromatography requires high-resolution pressure or flow control to provide stable conditions for measurement. The process - also called "GC" - utilizes inert gas (carrier) to move various compounds through "sticky" columns and record the time it takes for each compound to arrive at the detector. The speed at which each element reaches the sensor is the primary metric used to identify the individual compounds. The effectiveness of this process relies heavily on the mass flow rate remaining stable and constant, often during varying temperatures. If the flow rate is not steady, it becomes the most significant variable, obstructing detection of the compound. The dynamic nature of this process demands proportional control that both senses and reacts to the smallest changes in pressure or flow.
Lastly, resolution matters when printing matter. The concept of 3D printing is relatively mature. However, medical 3D printing with biologic material (bioprinting) is just being realized. Everything from blood vessels to skin, bone, and cartilage to the first heart made from human cells has become a bioprinting reality. Some of the newest bioprinters employ high-resolution vacuum control to suspend the biomaterial during the printing process. This temporary suspension requires just enough vacuum to overcome gravity until the print head reaches its destination. If too much vacuum is applied, the biomaterial withdraws too far from the nozzle, disrupting the timing and potentially reaching and damaging the controller. Too little vacuum and the excess material destroys the print.
Improving Resolution
A proportional controller's resolution - like its accuracy, repeatability, and stability - are greatly affected by the PID (proportional-integral-derivative) settings driving the device. These settings manage the feedback mechanism and define power distribution and timing to the internal valves in the hopes of mitigating the effects of dynamic process conditions. The PID parameters must be tuned appropriately to the specific application for the best resolution.
Ordinarily, proportional control devices receive their initial PID tuning at the factory during calibration. Some proportional control manufacturers offer excellent application assistance. Clippard is one such manufacturer.
The best way to improve resolution - as well as accuracy and repeatability - is by providing a complete and accurate picture of the specific process. When contacting Air Engineering and Supply technical support, supplying as much of the following details is critical to proper valve operation and setup: downstream volume, minimum and maximum inlet pressures, media, operating and ambient temperatures, minimum and maximum flow requirements, and general process conditions, like static or constant flow. Full application details allow Clippard's engineering team to optimize the PID settings, resulting in optimized performance.
Resolution Resolved
Understanding resolution and its impacts on proportional control applications are just one of the many concepts worth grasping when choosing an electronic proportional controller. While many applications may not require a high-resolution device, no process would suffer from better resolution - and in some instances, unexpected refinements may reveal themselves, elevating your product above the competition.
If you have questions about resolution or want to learn how Cordis can improve your process, contact Air Engineering and Supply today.